Traditional Block Printing
Hand printing is a special and revered art. It offers a unique and limitless approach to manufacture clothing, using traditional, slow methods.
We believe block printed fashion has beauty, charm and substance. Each garment is unique, due to the organic technique of hand printing.
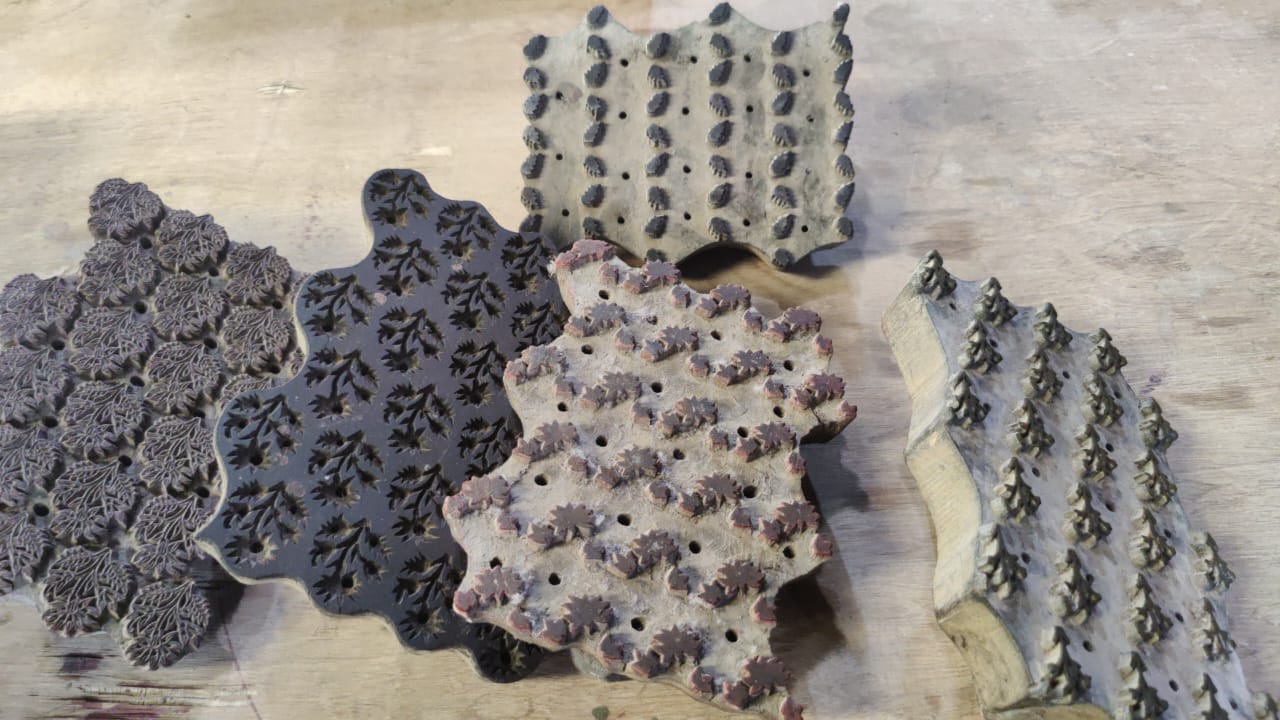
CARVING THE PATTERN ⚘
The first step to any block printing process is to create the pattern. The artisan places tracing paper with the pattern on, over a wooden block, and then uses a hammer and chisel to carve the pattern into the wood. This can easily take several days to complete the process. Once finished, a wooden handle is attached on the reverse side, like a stamp, which allows the artisan to push the block onto the fabric.
One pattern can require several blocks, this motif on the left is made up of a total of 5 blocks, for the filling colour, outline, petals and so on.
COLOUR PREP ⚘
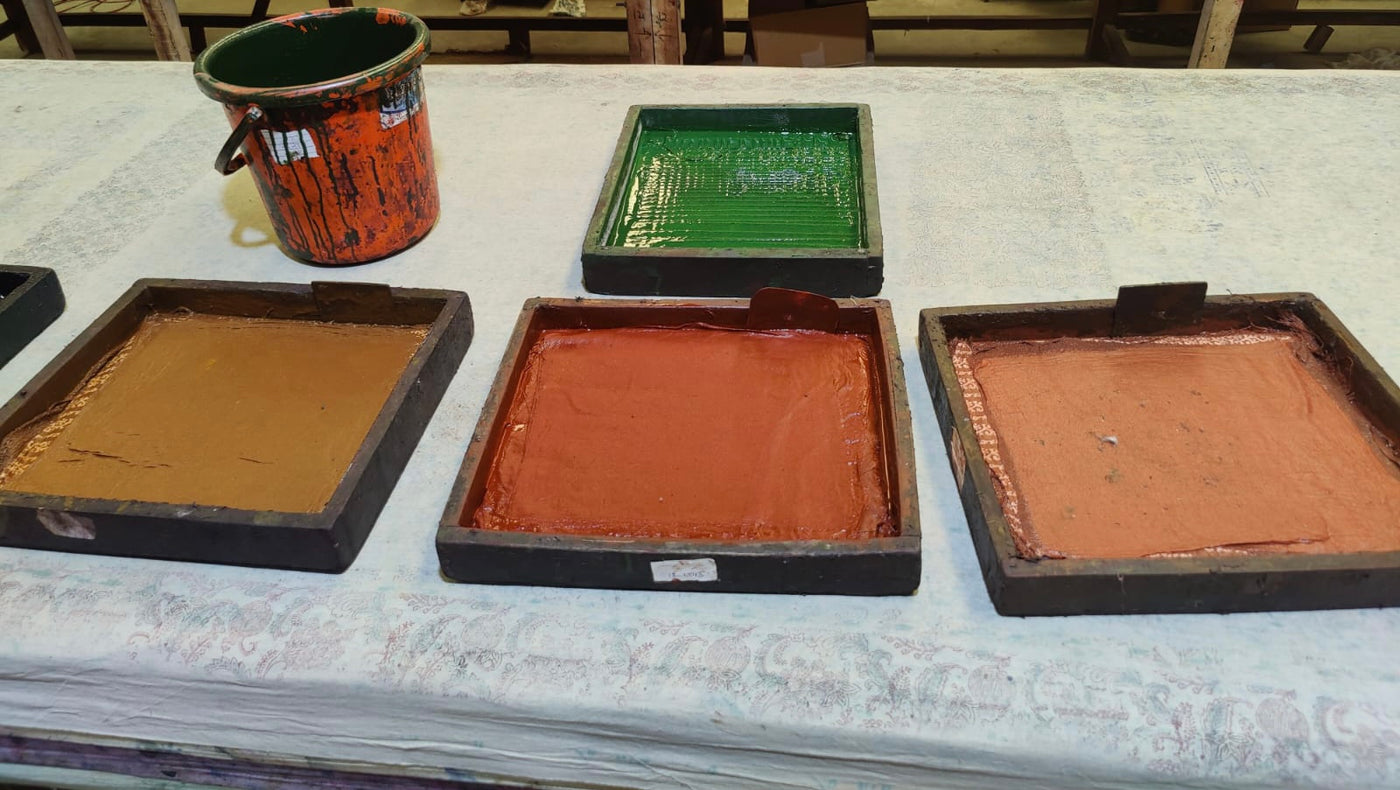
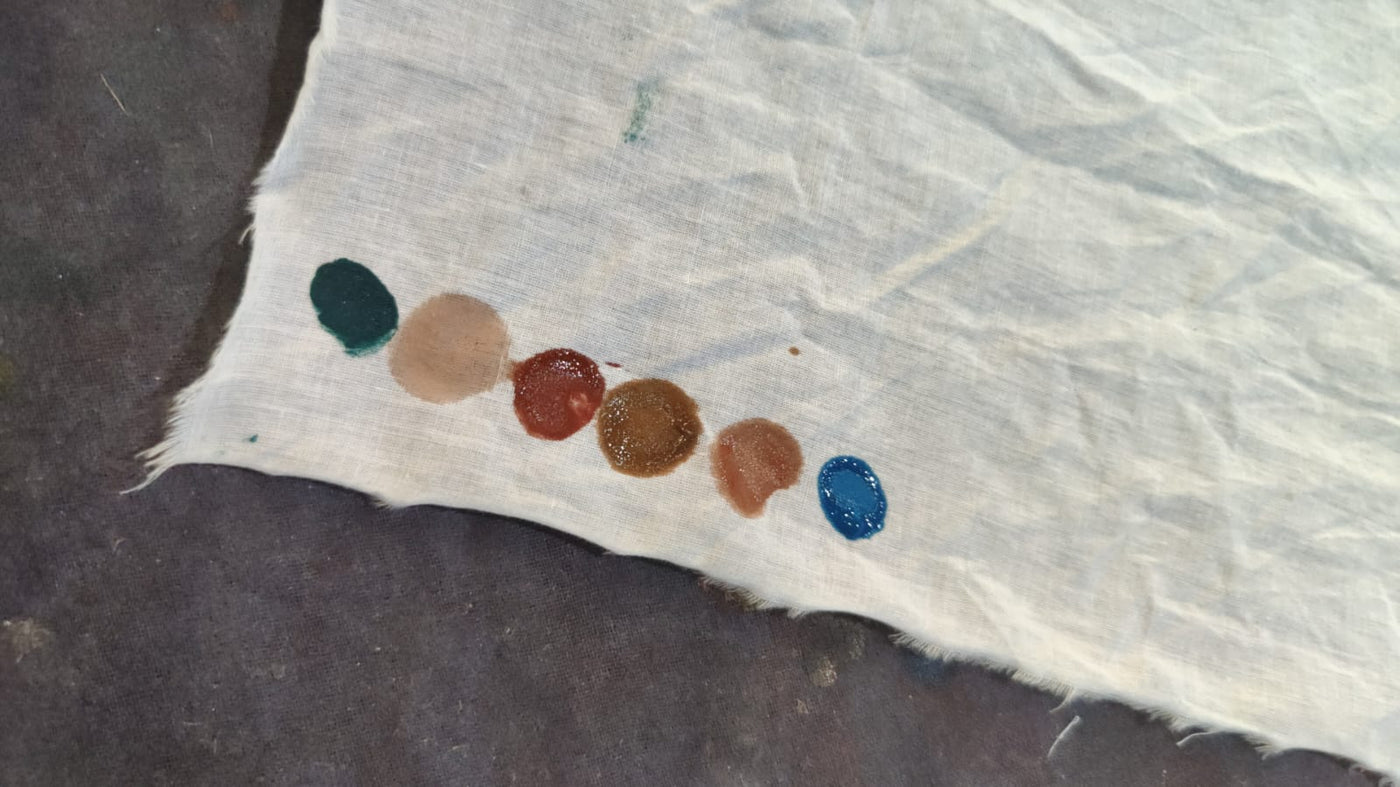
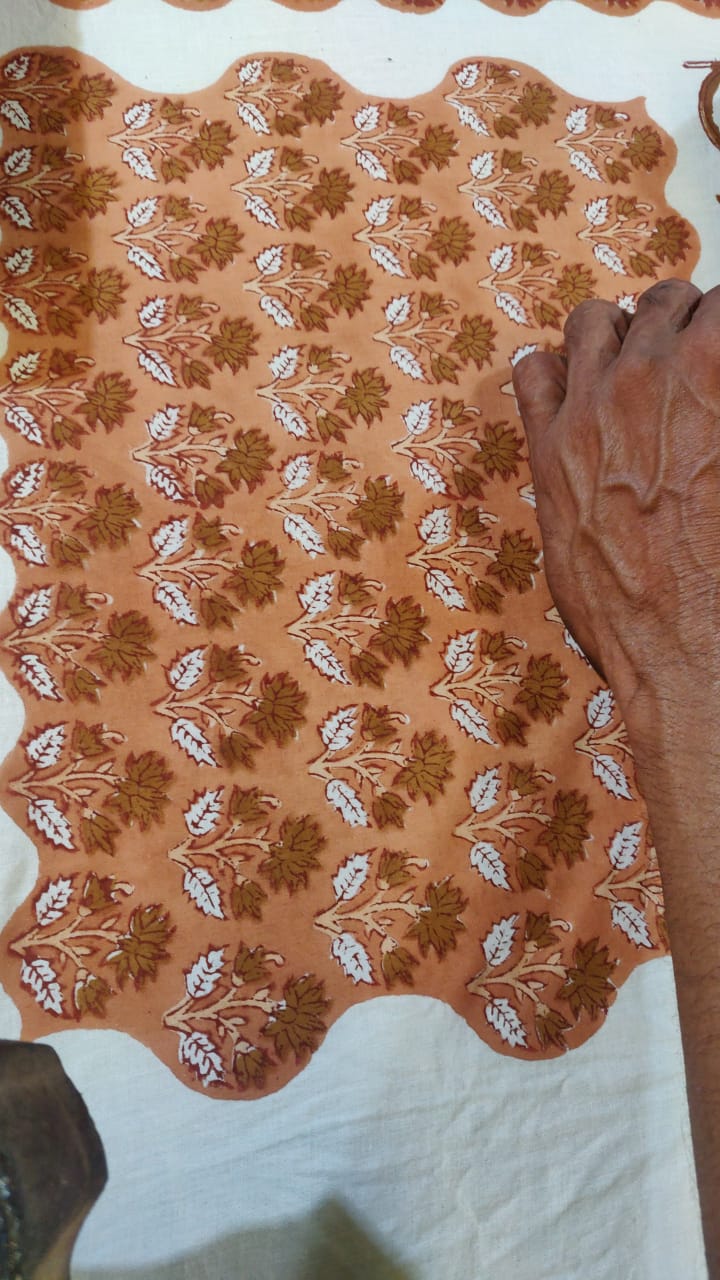
PRINTING ⚘
Once the desired colours are achieved (and there are several hundred shades you can create) they are ready for the printing process.
The blocks are then dipped into the colour tray (a different block is used for each individual colour) and then printed onto the fabric. No chemicals are used in the process of making colours or with printing with them.
It's a labour intensive and timely process. Skill, patience and precision is needed. Our block printers are masters at what they do, with expertise shared from many generations.
DRYING ⚘
Once the fabrics are printed, they are kept for 24 hours at room temperature, and then later washed.
They are hung out to dry, basking under the glorious sun.
The end colour results are very much dependent on Mother Nature. The weather can influence how light or dark a shade turns out. When it rains it's not possible to block print. We carefully time Monsoon periods so that we can work together with the seasons to produce our products.